This article originally appeared in Fleet Management Weekly
By Hasnain Jetha
Senior Procurement Manager
We’ve gone from COVID, to supply chain shortages, to rising inflation and on to the lingering effects of all of them. It feels like too long and due to many contributing reasons, it has been too long. Sometimes it’s difficult to muster up the necessary patience needed to do our jobs in this industry, yet “patience” should be the mantra of our age. We live in an interconnected global economy that is emerging from some complicated times and it is the impact of many elements that has brought us here. None of these things happened in a vacuum, which makes any solution that much more complex. So, lets address some of the questions we are all asking.
How long will the chip shortage continue?
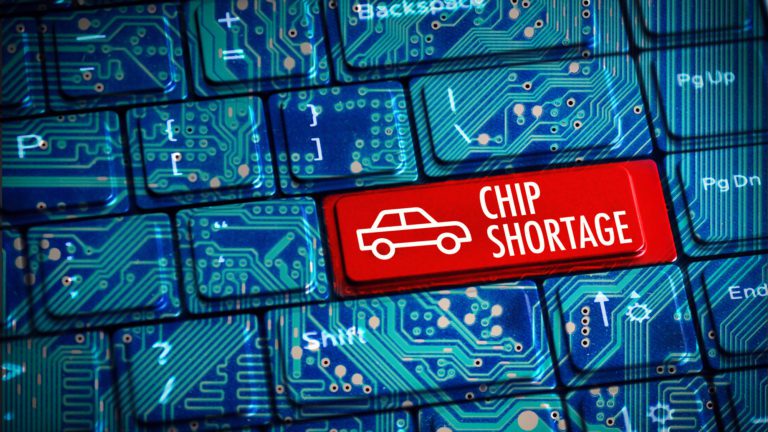
While there are some indicators that the chip shortage could be easing, experts still foresee challenges well into 2023. One factor that could contribute to a return to normal would be an easing of consumer demand. However, so far, we are still seeing post-COVID pent-up demand continue to fuel ordering.
How did we get here?
The supply chain issues that we are still feeling came to a head in 2020 and were the result of factors that were emerging just as the shut-downs occurred.
Leading up to the pandemic, demand for semiconductors was already approaching the full manufacturing capabilities of existing plants. As pandemic-era production shifted to consumer goods, very little excess manufacturing capacity was left. In late 2020, when vehicle orders unexpectedly rebounded and auto manufacturers urgently needed to re-instate canceled chip orders, the manufacturing capacity had been committed to other industries.
Why not simply ramp up chip production?
A timeline of three to six months is needed for chip manufacturers to retool for production of a specific chip; it takes years to build a microprocessor plant from the ground up.
As vehicles become more complex, incrementally more chips are needed. Many of the chips used in a vehicle are actually in the components built by suppliers who also need to source them—lengthening the complexity of the supply chain and delaying acquisition of parts. Added to this, are the geopolitical tensions that delay the sourcing of raw materials.
To compound the problem, it requires nearly twice as many semiconductors to build an electric vehicle. Additionally, there has been competition with the 5G rollout, which needs the larger chips most often used in vehicle production.
While the US invented the semiconductor, over the past three decades chip production has moved overseas. In 1990, 37 percent of the world’s semiconductors were produced in the US; today production here has declined to12 percent.
In reaction to the shortages, Congress has passed the CHIPS Act which was signed into law on August 9th, 2022. Among other initiatives, the act provides incentives for semiconductor research and manufacturing in the US—including production of the legacy chips needed for automobile manufacturer. The act is intended to have long-term impact by limiting US dependency on foreign chips through bolstering domestic production.
When will OEM production schedules return to normal?
The expectation is that heavy demand and limited supply will continue through this year and force OEMs to cut off ordering early or extend production. This will most likely persist through MY2023 and possibly into MY2024. Many of the OEM’s have taken an “allocation only” approach to MY2023 ordering by restricting orders of some or all models to certain clients and volumes—particularly to their legacy customers.
As we emerge from this crisis, full production recovery is impacted by pent-up demand. The expedient fix of purchasing vehicles from dealerships, “stock purchases”, as was previously done, is no longer a viable option as they are also experiencing shortages and have a need to protect their retail business. Vehicle manufacturers are working to fairly allocate vehicles to current customers to the best of their ability.
Once vehicles are built, what is behind the delivery delays?
Once a vehicle order is fulfilled, there are often shipping delays. The supply chain disruptions, skilled driver shortages and fuel pricing have also impacted the vehicle transport industry. As vehicle manufacturers shift production schedules, transporters need to shift their own schedules and staffing—often on very short notice. Vehicle transport is an industry that has always relied on predictability and that lack of predictability impacts efficiency. The current erratic day-to-day demand for transport services creates challenges which result in unavoidable delays.
What other impacts are there on the supply chain?
There are many disparate factors that can impact the automotive supply chain. In an effort to understand the complexity of an already vulnerable automotive supply chain, we also must pay attention to geopolitical occurrences and the effect of climate, both of which can impact the sourcing of raw materials and the global supply chain. Some current examples are:
- While the potentially disastrous US rail strike has been averted, the UK is facing rail, container port and dockworker strikes.
- Climate disruption is beginning to impact river freight in portions of Europe. In some cases, barges with coal and raw materials are running at 25% of full capacity.
- The Shanghai (China’s largest) and Ningbo ports can be impacted by typhoons. The most recent shut down was just a few weeks ago.
- With the winter coming, we could face COVID delays for shut-downs.
- The conflict in the Ukraine has impacted exports from both Ukraine and Russia.
As we started by mentioning, none of the supply chain impacts happen in a vacuum. If they did, we could look to one simple fix. However, our global supply chain is more complex than that and the repairs will take time, planning and patience. At Wheels Donlen we monitor all impacts to the supply chain and acknowledge that this continues to be an environment that demands agility.