Blog Post
Tips for Proactive Fleet Maintenance in Today’s Economy
By Jeff Sproat
July 7, 2022
Introduction
Do you feel the impact of multiple global economic factors on your fleet’s operating costs?
High oil prices have impacted the price of fuel, tires and oil changes. The chip shortage has been ongoing for over a year, and there’s no sign of it resolving soon. We’re seeing parts delays across the country and labor shortages in the repair industry, which means shops are operating at reduced capacities.
In short, it’s a tough environment for fleet managers right now, especially when it comes to maintenance. But it doesn’t have to be this way if you’re proactive about your fleet maintenance planning and use all the tools at your disposal to lower costs and minimize downtime.
That’s why we’ve put together this list of 5 tips for proactive fleet maintenance. Adopting these strategies will help improve your fleet’s safety, reduce vehicle downtime and ultimately enhance fleet productivity.
What is proactive maintenance?
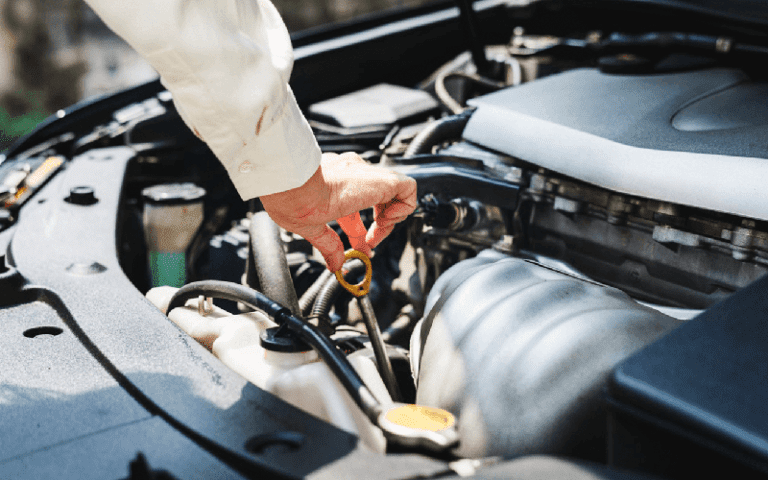
The first step in proactive maintenance is to understand the specific needs of your business. You must know what kind of equipment you have and how it operates in order to make informed decisions about when to service or replace a system or part. By focusing on prevention rather than reaction when something goes wrong, you’ll increase uptime while saving money.
Assess your fleet
While some fleets are keeping vehicles longer these days, others are cycling their assets more frequently. In either case, it’s important to align their maintenance schedule with OEM guidelines that correspond with how your vehicles are being used.
If you’re using the same manufacturer’s schedule for all of your vehicles and they aren’t being used in the same way, you could put them at risk. It’s important to check the OEM’S schedule recommendations against your usage pattern.
If a vehicle is driven more often than average, has a higher number of stop-and-goes than normal, or is driven further distances each day than normal, it may require more frequent service intervals than what is specified by the OEM guidelines for standard use.
For long-term fleet owners, it is beneficial to evaluate how long you plan to keep your vehicles in service. If you expect to keep the vehicle past 100,000 miles, we recommend you have a transmission flush or coolant flush added or reevaluated, based on OEM recommendations for your preventative maintenance schedule.
Know your OEM guidelines
If you’re not following the proper OEM recommendations for your driving patterns, your vehicles are likely to have more problems, which can lead to additional costs down the road. Following OEM guidelines is a good way to reduce costs and keep your fleet running smoothly, especially for things like routine maintenance schedules, fluid levels, and tire pressures.
Check Your Driver’s Compliance
Don’t forget about those compliance checks! Are your drivers performing their scheduled maintenance? Does it comply with local regulations? Is it in line with your fleet policy? If you find your drivers are continually getting services performed late, this can lead to higher repair costs as the vehicle ages.
We also recommended transitioning from an oil change only-type vendor to a full service vendor that has a more detailed multi-point inspection, as normal wear and tear items can be overlooked.
Ensure Your Maintenance Schedules Are Current
Make sure you are using the latest version of your vehicle’s maintenance schedule and service information, as well as any updates that the manufacturer has issued. The last thing you want is for an emergency to arise and not know what needs to be done. This will help ensure that your vehicles are running safely, reliably, and in a cost-effective manner.
Make Time for Planning
Under the best of circumstances, fleet maintenance is a task that requires planning. Even in today’s economy, it is important to understand how much maintenance work your fleet needs and when that work needs to be done. This means setting aside time every year to do an audit of all vehicles in your fleet to create a schedule for minor and major repairs.
Don’t wait for a problem to occur; work with your drivers to schedule regular maintenance appointments; this will enable you to address minor issues before they lead to larger ones that could cost thousands of dollars and delay business operations. Not only will this ensure better safety but also lower costs in the long run!
Finally, schedule enough time for service by understanding what services are needed and how long they will take. This is where we most commonly see drivers skip key services because they fail to plan ahead, or they did not expect the extra time required for a transmission service versus an oil change.
Conclusion
With the economy in a state of flux, fleet managers may look for ways to cut costs. However, there are smart ways to ‘cut costs’ that don’t involve neglecting basic maintenance for your fleet. By approaching preventative maintenance as a proactive plan rather than simple reactive measures, you will find the entire process of managing your fleet more efficient and cost-effective. Implementing these five tips will help you and your company get more during the challenges of today’s market. At Wheels Donlen, we are always available to answer questions you may have about keeping your fleet running smoothly. Contact us to learn more.